Conqueror Tonearm Mk4
“The obvious choice for Most Wanted Component of the Year.” Stereo Times
£3,100
Award-winning Conqueror Tonearm
“The obvious choice for Most Wanted Component of the Year.” Stereo Times
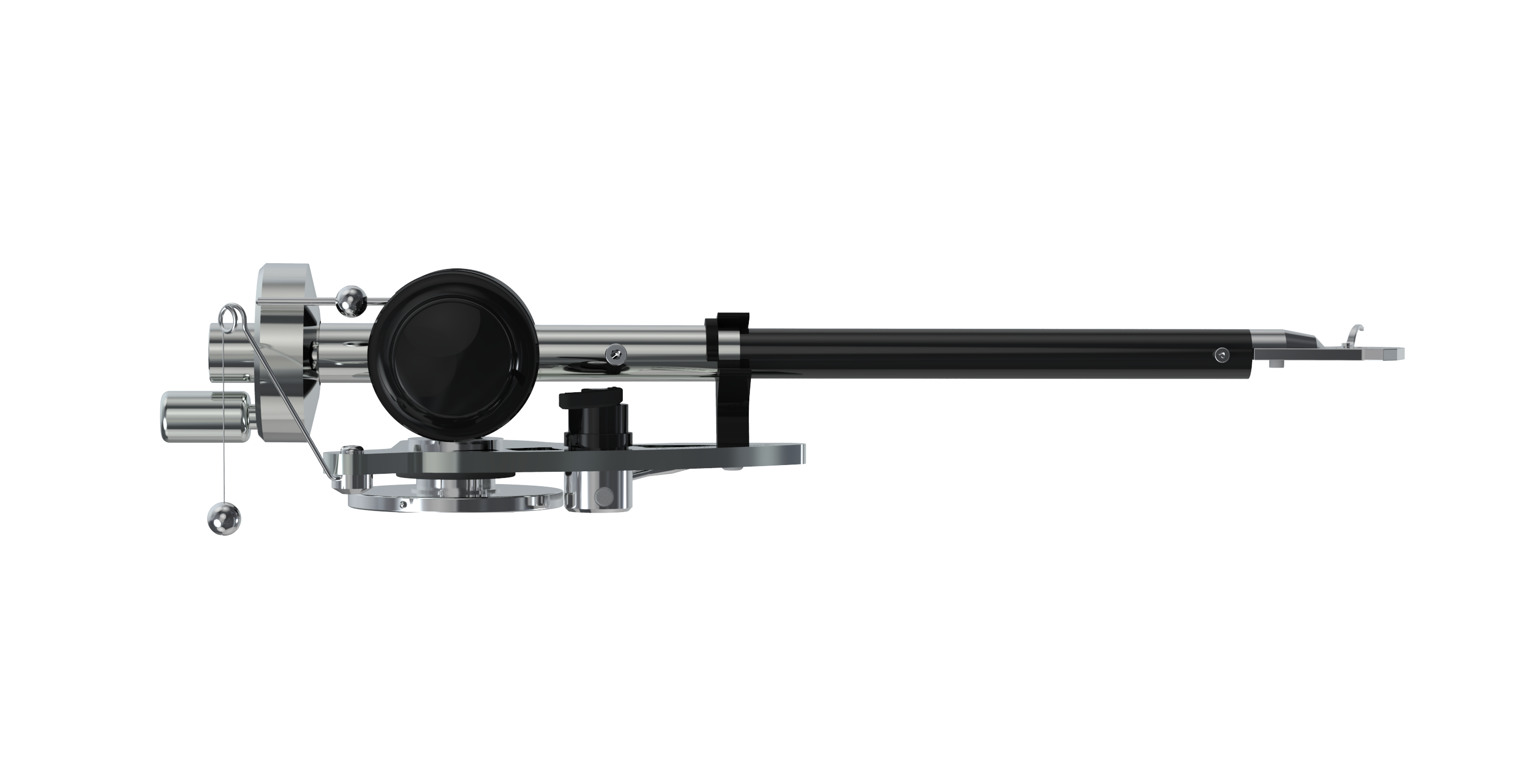
REVIEWS
“It builds on a very accomplished design and takes it – probably – about as far as it can go. The result is a wonderfully easy, open and even sound that has the uncanny ability to pull you into the music rather than tell you how good it is in microscopic detail.”
Read the full review >
Hi-Fi World
“I have bought the arm sent for review and am now in a seventh heaven of completely rediscovering my substantial, well looked after music collection.”
Read the full review >
Chris Breunig
“It merits the highest of recommendations and is the obvious choice for Most Wanted Component of the Year. Simply, the Conqueror is in a class by itself.”
Read the full review >
Stereo Times
“Stunning. Space prohibits me from detailing every improvement I spotted over the Illustrious, and every difference I heard against the SME Series IV, but suffice to say that this is one of the very best tonearms yet made by anybody.”
Read the full review >
Hi-Fi World
“Having definitively surpassed what many consider to be the best tonearm in the world, I expect the Conqueror to be in permanent residence in my reference system.”
Read the full review >
10 Audio
On Saturday I collected the Conqueror arm and installed it to the Oracle. I have never heard one of your products before and I hoped that it will be slightly better than my SME V (as promised in some reviews).
But it was a shock to find out that the years with the SME were lost years. Your product betters the SME in each aspect. It is outstanding! Because of this experience, I will go to Mr. Schmitz (Munich) to hear your decks next time. Read more owner comments >
Andreas Winter – Bochum, Germany, Owner Comment
REVIEWS
“It builds on a very accomplished design and takes it – probably – about as far as it can go. The result is a wonderfully easy, open and even sound that has the uncanny ability to pull you into the music rather than tell you how good it is in microscopic detail.”
Read the full review >
Hi-Fi World
“I have bought the arm sent for review and am now in a seventh heaven of completely rediscovering my substantial, well looked after music collection.”
Read the full review >
Chris Breunig
“It merits the highest of recommendations and is the obvious choice for Most Wanted Component of the Year. Simply, the Conqueror is in a class by itself.”
Read the full review >
Stereo Times
“Stunning. Space prohibits me from detailing every improvement I spotted over the Illustrious, and every difference I heard against the SME Series IV, but suffice to say that this is one of the very best tonearms yet made by anybody.”
Read the full review >
Hi-Fi World
“Having definitively surpassed what many consider to be the best tonearm in the world, I expect the Conqueror to be in permanent residence in my reference system.”
Read the full review >
10 Audio
But it was a shock to find out that the years with the SME were lost years. Your product betters the SME in each aspect. It is outstanding! Because of this experience, I will go to Mr. Schmitz (Munich) to hear your decks next time.
Read more owner comments >
Andreas Winter – Bochum, Germany
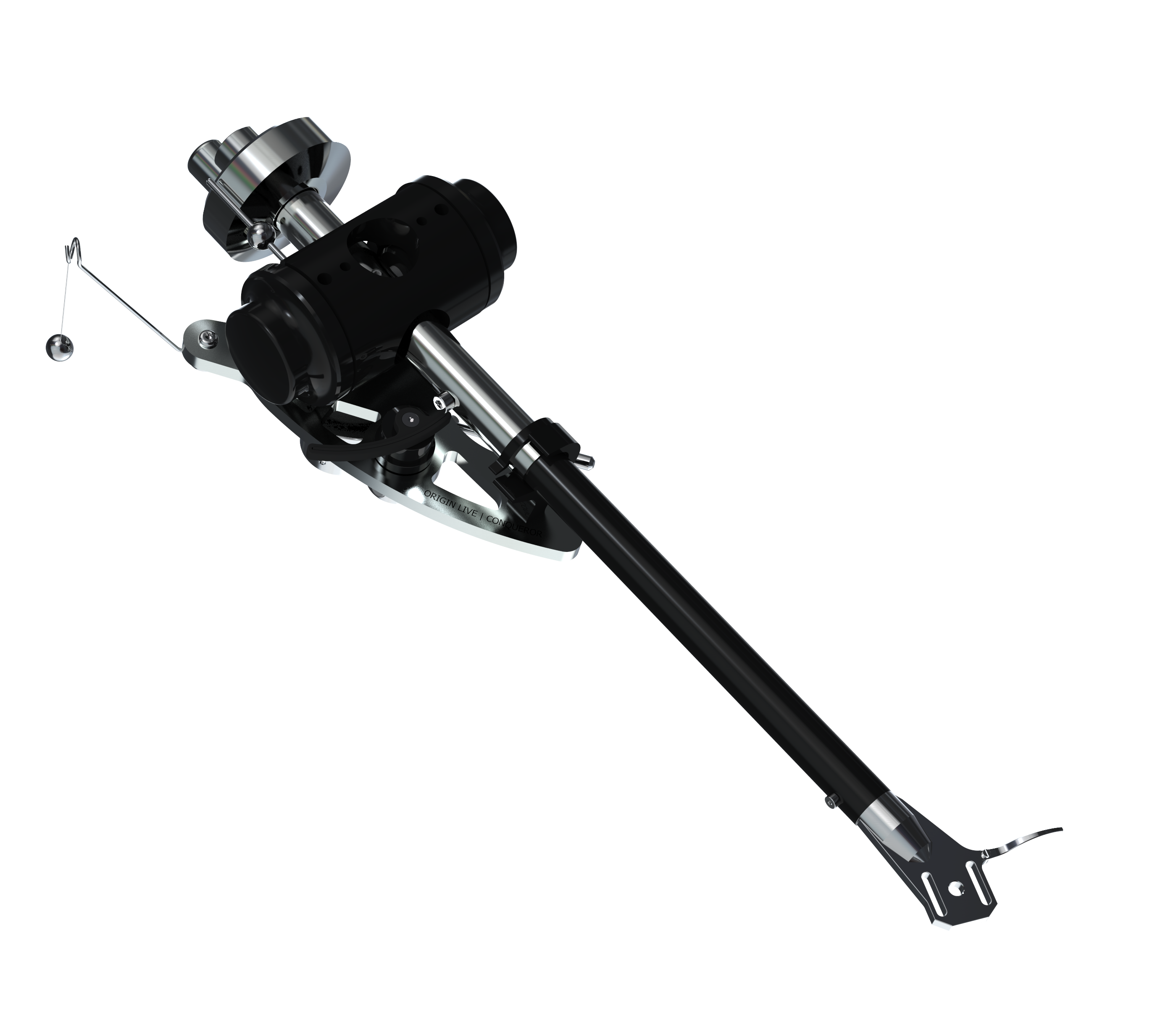
Description
One of the very best tonearms on sale at any price aptly named the Conqueror. Yet, this isn’t an overblown or showy performer – it’s not voiced to impress some of the people, some of the time. Rather, it’s exceptionally even-handed and balanced in its presentation and sounds sublime across a wide range of music. An immensely high resolution measuring instrument, it is nevertheless consummately musical and organic sounding. A real ‘fit and forget’ product, no matter what you play, it just dissolves away.
Compared to more affordable Origin Live tonearms, there’s an obvious increase in transparency, and with it a heightened sense of realism. Music sounds more natural and less processed as if a bright light has been shone on the recording and it’s there in front of you, in all its glory. Yet it confers an uncanny smoothness on the music, too; there’s a wonderful sense of ease and rhythmic ebb and flow. Bass is yet more powerful and defined than Illustrious, which is no small feat. Vocals shimmer with natural timbre and stereo imaging is almost holographic.
Warranty
We guarantee arms to be free from fault for 5 years and will undertake remedial work, providing the arm has not been modified by any party other than ourselves. This warranty does not cover abuse or mistreatment, which includes neglecting the instructions in the owner manual.
Description
One of the very best tonearms on sale at any price aptly named the Conqueror. Yet, this isn’t an overblown or showy performer – it’s not voiced to impress some of the people, some of the time. Rather, it’s exceptionally even-handed and balanced in its presentation and sounds sublime across a wide range of music. An immensely high resolution measuring instrument, it is nevertheless consummately musical and organic sounding. A real ‘fit and forget’ product, no matter what you play, it just dissolves away.
Compared to more affordable Origin Live tonearms, there’s an obvious increase in transparency, and with it a heightened sense of realism. Music sounds more natural and less processed as if a bright light has been shone on the recording and it’s there in front of you, in all its glory. Yet it confers an uncanny smoothness on the music, too; there’s a wonderful sense of ease and rhythmic ebb and flow. Bass is yet more powerful and defined than Illustrious, which is no small feat. Vocals shimmer with natural timbre and stereo imaging is almost holographic.
Warranty
We guarantee arms to be free from fault for 5 years and will undertake remedial work, providing the arm has not been modified by any party other than ourselves. This warranty does not cover abuse or mistreatment, which includes neglecting the instructions in the owner manual.
Features
Yellow stars denote new features not present on lower models.
Higher-strength Arm Tube
The high-grade aircraft alloy tube is further stiffened with carbon fibre. It is also reinforced using a long rear stub sleeve which is carefully interfaced to provide maximum energy dissipation and minimal reflections. This frees up your cartridge to perform as it should, away from the colouration and disruption caused by resonance and reflected vibration.
Rigidly Attached Counterweight
The counterweight attachment has been carefully engineered to hold the arm tube more rigidly for cartridge stability whilst at the same time decoupling itself to minimize energy reflection back down the tube. The results are clearly heard in improved dynamics and a sense of power and control in the bass.
Dual Pivot Bearings
For vertical arm movement, the bearings consist of Ultra-hard tungsten carbide points sitting in hardened and burnished steel cups. This combination not only delivers incredibly low friction levels but is also much more robust than jewelled bearings which tend to shatter under stress. The results are incredible transparency, fluidity and retrieval of fine detail.
Rhodium-plated Single Point RCA Plugs
After testing numerous high-end RCA plugs these were selected for their outstanding performance. Single point contact has the advantage of reducing eddy currents and Rhodium with it’s ultra-smooth surface seems to provide a better interface in electrical joints.
Features
Yellow stars denote new features not present on lower models.
Higher-strength Arm Tube
The high-grade aircraft alloy tube is further stiffened with carbon fibre. It is also reinforced using a long rear stub sleeve which is carefully interfaced to provide maximum energy dissipation and minimal reflections. This frees up your cartridge to perform as it should, away from the colouration and disruption caused by resonance and reflected vibration.
Rigidly Attached Counterweight
The counterweight attachment has been carefully engineered to hold the arm tube more rigidly for cartridge stability whilst at the same time decoupling itself to minimize energy reflection back down the tube. The results are clearly heard in improved dynamics and a sense of power and control in the bass.
Dual Pivot Bearings
For vertical arm movement, the bearings consist of Ultra-hard tungsten carbide points sitting in hardened and burnished steel cups. This combination not only delivers incredibly low friction levels but is also much more robust than jewelled bearings which tend to shatter under stress. The results are incredible transparency, fluidity and retrieval of fine detail.
Rhodium-plated Single Point RCA Plugs
After testing numerous high-end RCA plugs these were selected for their outstanding performance. Single point contact has the advantage of reducing eddy currents and Rhodium with it’s ultra-smooth surface seems to provide a better interface in electrical joints.
People often ask 2 questions.
Firstly, which arm is best for my particular deck and/or cartridge?
The answer is simply that all Origin Live arms work well with all decks and cartridges. Unlike many arms, there are no synergy or compatibility issues to consider.
Compliance: If you wish to optimise your cartridge compliance with the arm, we offer headshell weights of 2, 5 and 10 grams. Compliance matching is audible but of relatively minor importance compared to other factors in arm performance. Testing reveals that a poor compliance match with a better arm design will track and perform much better than a lesser arm with a perfect compliance match.
Secondly, how much should be invested in an arm due to the law of diminishing returns?
This question is more involved and the following points may help in coming to your own conclusions.
- There is no point at which you will stop hearing the difference a better arm makes, regardless of your system.
- Better arms reduce record wear due to reduced “chatter”
- You get significantly better performance £ for £ upgrading an arm than you would by investing the same on a Cartridge.
- Owning a better arm means you achieve better performance whilst running much cheaper cartridges. in the long run, this represents significant savings every time you need to replace your cartridge.
- Consider a balanced investment across components in the front end of your system. If your phono stage is poor then you are best off budgeting proportionally. For Origin Live turntables we recommend front end split should be approximate:
30% Turntable, 30% Tonearm, 30 % Phono-Stage, 10% Cartridge - Compare Origin Live tonearm features
Origin Live arms can fit most decks thanks to 4 length options and mounting adaptors.
For Rega arm mounts (221mm effective length arms) – Origin Live arms have a threaded base mounting that fits all arm-boards designed for Rega arms. This is literally a fuss-free drop-in replacement with no modifications needed, regardless of whether the Rega arm has a threaded base or 3 point mounting. This is the simplest case so we put it first. Rega arms and their modified versions (i.e Michell, NAD etc) are easy to replace with an Origin Live arm. All standard length (239mm) Origin Live arms will fit directly into all standard Rega armboard mounts. No additional holes are needed, no modifications, no extra fittings, no VTA adjusters. This easy swap is down to the geometry of Origin Live arms being identical to all Rega arms. It makes no difference if the Rega mount you have is the later 3 point mounting or earlier single hole mounting. Neither does the model number or vintage of a Rega arm make any difference. The only question some people raise after fitting their Origin Live arm is that 3 mounting holes remain visible if the mount is the 3 point type of Rega mount. The solution to tidy up the looks is either to fill the 3 holes with dummy round head M3 Allen bolts or you can order a 1mm thick Formica black disc from us to cover the holes > see link Disc to cover 3 Rega mounting holes. Other solutions include simply cutting a cover disc from a black card or thin plastic. Armboards & Mounting Position Hole Diameter: You can fit Origin Live arms to any deck but sometimes your armboard may need modification or changing to a new one – (contact a dealer or the turntable manufacturer for the second option). The tonearms require a single hole in the armboard or plinth – from 23mm to 25mm in diameter (23mm is ideal for accurate fit). If the hole in your armboard is say 1mm or more oversize then all you need to do is centralize the arm in the hole. For best performance, you do not want a tight fit and so all you need to do is put a rubber band or wrap a shallow strip of card around the arm base – anything that will act as a spacer – it does not need to be machined sleeve. Armboard Thickness: Once the arm is inserted through this hole, you secure it with a large nut under the armboard which clamps it in position. The armboard can be any thickness up to 25mm for this to work. The distance from the centre of the armhole to the centre of the platter spindle needs to be 222mm plus or minus 1mm. The arms can rotate to be clamped at any angle. The effective length of the arm from its mounting hole centre to the cartridge end of the arm is 240mm. The arm protrusion from the pivot point to the rear is 50mm to the end of the counterweight stub. For Encounter Arms and Above – If the top of the armboard is around 24mm below the top of the platter then the arm will be at its lowest position for tracking a normal cartridge (17mm body height) and can be raised by a further 14mm For 12-inch Arms Only – Centre of 23mm – 25mm diameter hole for arm mount to centre of platter spindle is 295.6mm plus or minus 1mm. The length of the arm from its mounting hole centre to the cartridge end of the arm is 309mm. The overhang from the pivot point at the rear end is 50mm to the end of the counterweight stub. Note: Cartridge alignment is at best only ever a compromise. A cartridge is only aligned at 2 points on the record – For the remainder of positions on the record it’s out of alignment – We say this to save fretting over the last 0.5mm accuracy and give a bit of perspective. Alignment makes an audible difference but on the scale of other parameters, it’s really not a lot. For Linn style arm mounts (211mm effective length arms) – We offer predrilled arm-boards for fitting our standard arms (221mm effective length) to the Linn LP12. Alternatively, we offer our arms with Linn geometry (211mm effective length) and Linn style 3 bolt base mount. This allows our arms to work as a simple drop-in replacement for all Linn arms and those which follow this geometry. If you have a Linn LP12 turntable with a Linn arm then the armhole on your current armboard will be in the wrong position (Linn arms mount at a distance of 211mm from the platter spindle). We can supply you with a Pre-drilled armboard for the Origin Live and Rega arms at £27 – this board is identical to the Linn armboard but is missing the Linn Logo. Alternatively, you can get a blank arm-board from Linn and get it drilled. This is simple to fit. On newer Linns the wooden corner brace has been increased in size which creates a slight foul with Standard size Origin Live and Rega arms. This is easy to rectify by removing a small semi-circle of the brace. Probably the quickest way to achieve this is to drill a series of 4mm holes as close as possible to one another in the shape of the cut out you need. Then finish off the job with a chisel. After fitting a new arm you can find printable instructions for setting up your Linn at Linn Sondek LP12 turntable instructions Alternatively, you can order all Origin Live arms with “Linn geometry” – see arm options in the ordering process. This means the arm effective length is manufactured as identical to Linn geometry. We also provide a sleeve/base which allows you to fit Origin Live arms directly to your existing Linn arm board. This overcomes the problem with some later Linn decks where the armboard is integral with the sub-chassis and thus non-detachable. For SME arm mounts – you can fit our bolt-on SME adaptor which means the arm can be fitted to any SME arm-board. If your arm has an SME mount there is an adaptor plate available on this website which bolts to your existing mount and provides the correct hole and position for mounting Origin Live arms – see Accessories > Vinyl > Adaptors Modifying Your Current Arm Board If you modify your current armboard you will need to cut a hole in the board to locate the arm at the dimensions given above. This will leave you with the old hole looking unsightly. To hide this, make up a large circular plate washer of black card, aluminium or other material and glue this to the armboard – the spacing washers we supply with a new arm have an outside diameter of 48mm and will normally fulfil this function for most situations (the thickness of the washer is 1.5mm or 4mm). The advantage of glueing the washer to the armboard is that it also locates the arm in the correct position. Arm Heights For Enterprise to Renown Min | Max height between the top of armboard and underside of headshell is 40mm to 55mm (i.e 15mm upward adjustment) For Encounter to Conqueror arms Min | Max height between the top of armboard and underside of headshell is 39mm to 54mm (i.e 15mm upward adjustment) For Alliance to Zephyr When fitted to a 4mm thick armboard – The height between the top of the armboard and the underside of the headshell is 43mm(i.e 30mm upward adjustment). For every 1mm extra thickness of the armboard deduct 1mm from upward adjustment (30mm). Cartridge heights normally vary from 15mm to 18mm with 17mm being the average
Click here to expand Fitting to a Rega Arm Mount
* You need not worry about VTA for Encounter arms and above as they have integral VTA adjustment.
* Arms below Encounter use VTA adjustment on the arm mounting thread itself so arm boards need to be around 20mm or less to allow adjustment.
Click here to expand Fitting to the Linn LP12
Click here to expand Fitting to an SME mount
People often ask whether a certain cartridge will match a certain Origin Live arm. In short, the whole issue of cartridge matching and compliance is irrelevant for our arms – All our arm models track every cartridge with ease (no exceptions) and handle high energy levels with equal ease.15 years of people mounting all types and brands of the cartridge (even Deccas – the hardest to track cartridge) have taught us this. Users attest that Origin Live arms are entirely at home with Dynavector, Kuoetsu, Lyra, Benz and any other brand you care to name.
Origin Live arms are probably unique in this aspect due to various damping tricks and handling of inertia. These overcome the problems which plague other arms.
Yes, compliance matching can help badly behaved arms but with a well-designed arm, it’s of very low significance and is best ignored.